WhatsApp is no longer just about messaging. With nearly three billion users worldwide, Meta is now layering artificial intelligence and monetisation tools into the…
Are 3D concrete printed houses the future past earthquakes?
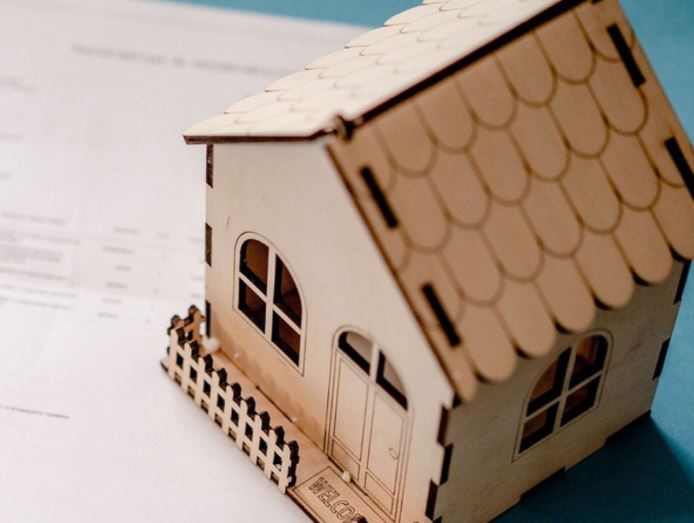
The South African Housing and Infrastructure Fund (SAHIF) has announced that 3D concrete printed homes are a plan that may withstand seismic activity following a tremor this week.
The SAHIF has confirmed that the innovative 3D-printed homes it planned to roll out across the country were able to withstand seismic activity.
A venture between SAHIF and Dutch construction technology company Cybe Construction seems to be a possible answer following this week’s tremor.
This week’s earthquake further illuminates the country’s need for resilient, sustainable, and quality housing says SAHIF CEO Rali Mampeule.
He adds that the technology has demonstrated the capacity to construct a complete house within five days, marking a significant stride towards addressing the country’s pressing housing deficit.
“Introducing these innovative 3D-printed, earthquake-proof homes offers a sustainable solution to the country’s housing shortage and reassures residents of their safety.”
Mampeule says the demand for affordable quality housing in the country outstripped the supply and the solution was to address the challenge by reducing the cost of material and labour, while speeding up the construction process to improve the overall quality of the house.
“Not only are 3D houses more affordable and time efficient to build, but we know they are durable enough to withstand the kinds of seismic forces that surprised us all this week,” he added.
This fourth industrial revolution technology of 3D concrete printing allows architects and engineers to design and create buildings that can absorb and dissipate the energy produced during a tremor.
The houses are structurally sound with earthquake-resistant materials such as steel and polymer.
The special ingredient here seems to be the high-strength earthquake-resistant concrete known as CyBe Mortar, formulated for 3D printing.
Couple that with the option to use graphene polymer from UK manufacturer 2-Dtech, the materials promise durability including flexibility, which is ideal for the construction of earthquake-proof homes.
Mampeule says the partnership’s mission was to provide affordable and rapid housing solutions using CyBe’s mobile 3D printer.
The addition of the technology does come with its challenges such as unemployment.
Those who risk unemployment may need to be reskilled and this will mean departments may need to strengthen their upskilling sectors.
The University of Johannesburg was a solid partner which saw the successful on-site training using CyBe’s mobile 3D concrete printer at the university recently, a solid indicator that shows that partnerships may have an impact on housing.
Professor Jeffrey Mahachi, Head of School, civil engineering and the build environment said the Univerity of Johannesburg was responsible for the procurement of the printer and the research such as testing the material.
This technology, prints a house in around 8 hours, in great quality he adds, while noting the universities goal to solve local problems.
Minister of Higher Education and Training Dr. Blade Nzimande said there was a challenge to balance the need to ensure that the construction sector gets back to its feet and the transition into the fourth industrial revolution.
This [the technology] doesn’t pose a threat to the construction sector he said.
“It provides possibilities, to build faster. t doesn’t take away all jobs. There will be people to do the foundation [of houses], roofing, windows and every other thing. For the construction sector it’s an opportunity [and] it is better to experiment with the opportunity now.
Also read: For the road tripper, creative vlogger, Samsung Galaxy A54 5G, A34 5G